So,
nun werde auch ich mal Anfangen meinen Bericht über die zwei vergangenen Tage in Markneukirchen schreiben. Ich hoffe, dass ich die jeweiligen Fakten so weit gut wiedergeben kann und mein Eindruck, wenn die Bilder auch eher gering und schlecht sind, euch trotzdem zeigt wie Warwick funktioniert und was wir alles geboten bekommen haben. Was die Bilder angeht, solltet ihr euch jedoch keine Gedanken machen, es ist bestimmt alles 3-4x fotografiert worden und sollte anderweitig vorhanden sein in besserer Qualität.
Zuerst aber noch einmal vielen Dank für diese Möglichkeit die uns Hans Peter Wilfer ermöglicht hat und für ganz Warwick und seine Mitarbeiter, was die Organisation dieser Tage anging und wie gerne sie unsere Fragen beantwortet haben.
Die Anreise
Nachdem mein Zeitplan am Sonntag eigentlich alles andere als geplant ablief und abends dann doch nicht so früh ins Bett kam, blieb mir mit Glück eine Stunde Schlaf, bevor ich um kurz nach 2 aus dem Bett gemüht habe. Der Start in den Tag war also etwas ermüdend. Aber das wurde dann so weit nicht ansatzweise ein Problem, wobei
später einmal kurz. Also fertiggemacht, zum Essen Hbf gefahren und Richtung Herne aufgebrochen um mich dort gegen ca. 4:30 mit Kort zu treffen und gemeinschaftlich die 550 km Richtung Markneukirchen zu fahren. Die Fahrt lief so weit eigentlich ohne Probleme und ein Stau war nicht ansatzweise zu sehen. Auch in Markneukirchen selbst sind wir trotz der ganzen Umbauten und Baustellen mit dem Navi ohne Probleme bis zum Hotel gekommen an dem bereits Nerezza eingetroffen war (welcher ja bereits Sonntag angereist ist). Im Abstand der Nächsten ½ Stunde trafen dann eigentlich auch abgesehen von Bierpreis und die Beiden Berliner die sich glaube ich etwas in Markneukirchen verfahren hatten alle ein. So das Wir es uns mit Kaffee, Apfelschorle, Wasser, Cappuccino etc.
erst einmal auf der Terrasse gemütlich machten und auf die anderen warteten. Hier kam dann auch die Erkenntnis, wieso es so viele Instrumentenbauer in Markneukirchen gibt, man hört nämlich eigentlich gar nichts. Was sich natürlich dann änderte, als wir Richtung Warwick aufbrachen.
Die Ankunft am Werk
Nachdem wir dann durch einen Schleichweg welcher uns durch den Wald führte, innerhalb von vielleicht 5 Minuten am Warwick Werksgelände ankamen wurde erst einmal ein Gruppenfoto vor der Tür gemacht.
Das Werk selbst scheint zwar von außen schon Modern zu sein und im Gegensatz zu den angrenzenden Firmen ansprechender anzuschauen aber wegen des äußeren waren wir ja nicht da, sodass wir uns dann doch recht schnell in das Werk begeben haben. Und dort fängt das Staunen dann bereits an, denn die Eingangshalle besteht eigentlich nur aus Tafeln mit den jeweiligen Signature Bässen der verschiedenen Künstler. Aber zuerst lernten wir Hans Peter Wilfer kennen, der uns begrüßte und uns schon ein paar kleine Sätze zum Ablauf des Tages mit auf den Weg gab. Daran anknüpfend konnten wir natürlich nicht gebremst werden und schauten uns die jeweiligen Signature Bässe an und spielten sie zumindest trocken. In den Showroom mit den Bässen und Verstärkern durften wir aber noch nicht, wer weiß ob sie Sorgen hatten uns dort wieder herauszubekommen

.
Die Werksführung
Einleitung
Nachdem der erste Raum so weit von allem grob inspiziert wurde, starteten wir auch direkt durch denn der Tag war ja noch lang. So wurden wir von Johannes, Marcus, Hans Peter Wilfer und zwei weiteren Medienmitarbeitern (Die Namen sind mir leider total entfallen) begleitet. Durch die obere Etage und Büros geführt mit einem etwas längeren Aufenthalt im Fitnessraum. Nicht, weil wir Sport getrieben haben, sondern weil man von dort eigentlich zumindest das Werk, das Holzlager und den Hof sieht und der Ort eigentlich durch die großen Fenster natürlich auch zu den ersten Fragen und Antworten führten. So kam natürlich auch das Thema auf die Lohn und Mitarbeiter Situation und wie die Absatzzahlen durch die Kampagne einiger gelangweilten Pressemitarbeiter mit Hetze gegen Warwick zu spüren waren (dies sind meine eigenen Worte!). Die Atmosphäre die auf uns traf, schien zumindest nicht irgendwie künstlich oder unter strenger Herrschaft mit Angst um seinen Arbeitsplatz und unzufriedenen Mitarbeitern zu stehen.
Etwas Allgemeines zu Warwick und dem Bau der Instrumente
Wie wir im Verlaufe des Gespräches erfuhren, sind bei Warwick ca. 70 Mitarbeiter beschäftigt, wovon 21 Mitarbeiter in der Produktion tätig sind 1995 waren es ca. 25-30.
Hans Peter Wilfer achtet sehr auf Qualität, wie er uns erzählte und dieser Schritt zieht sich auch durch die Produktion und findet bei verschiedenen Themen sicherlich auch Erwähnung, 0-Fehler Toleranz. Wer schlampt, darf sich damit auch gerne mal vor dem Chef äußern

. Wenn man die Instrumente jedoch sieht und auf die Details achtet, versteht man, was Qualität bei diesen Instrumenten bedeutet.
Die Zeit pro Instrument beträgt ca. 18-25 Arbeitsstunden, davon wird die meiste Zeit auf die Detailarbeit gerechnet (Konturen der Bässe z.B.). Außerdem wird nach jedem Arbeitsschritt eine Qualitätskontrolle durchgeführt, um Fehler früh zu erkennen und nicht mit einem fehlerhaften Instrument weiterzubauen. Die Anzahl der gefertigten Instrumente beträgt im Schnitt 100-200 pro Monat, diese Zahl schwankt aber saisonal, im Jahresdurchschnitt werden so ca. 1500-2000 Instrumente hergestellt. Die Dauer, bis ein Instrument nach Arbeitsauftrag das Werk verlässt, beträgt ca. 4-6 Wochen, bei einem Standard Modell sind es nur ca. 2.
Holz(lager) & Produktion (Hier vermische ich jetzt beide Tage etwas)
Holz(-lager)
Weiter ging es auf unserer Führung in das Holzlager, dessen Größe und Anzahl an verschiedenen Hölzern natürlich beeindruckt. Dort haben wir dann erfahren das Warwick ca. 40 Holzsorten im Angebot hat und die Lagerung min. 3-5 Jahre dauert, manches lagert aber auch schon viel länger, weil entweder die Nachfrage nicht da ist oder es keines, in der Warwick Produktpalette geführtes Holz ist (damit meine ich ein Model welches aus diesem Holz besteht, nicht auf Kundenwunsch gebaut wird). Weiter erfahren wir das Warwick sehr auf den Kauf von FSC Holz beim Einkauf achtet, dieses aber nicht in großen Mengen und darüber hinaus von dem meisten Hölzern auch gar nicht erst zu bekommen ist. Dazu kommen Probleme die, den Welt Holzmarkt betreffen und selbigen in den letzten Jahren stark beeinflusst haben, dazu gehören natürlich auch einige Weltkonflikte.
Warwick selbst kauft das Holz als Rundholzware und verarbeitet das Holz komplett für das eigene Bedürfnis. Dabei entstehen aus 1 m³ Holz ca. 25-30 Bodys. Der Verschnitt beträgt durchaus aber immer noch ca. 70%, was darin begründet liegt das Musiker kein Interesse an 10-fach verleimten Hälsen haben. Wobei man bei der Warwick-Qualität sicherlich bessere Ergebnisse als andere Hersteller bekommt.
Ein weiteres Highlight zum Thema Holz war sicherlich der zweite Tag und das Betreten des Raumes, in dem keine Fotos gestattet waren. Bei diesem Raum handelte es sich nämlich um das Custom Shop Holzlager, mit einigen sehr schönen Hölzern für den Bassbau, z.B. Buck Eye Burl, Zebrano, etc. . (das Nachfolgende Bild entstand in der Produktion und zeigt einige der Holzsorten)
Produktion
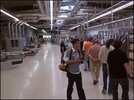
Weiter ging es mit der Produktion und wer die Halle das erste mal betritt wird nicht unbedingt von einem Holz verarbeitenden Betrieb ausgehen. Denn die Halle ist ebenfalls sehr Modern mit vielen Maschinen ausgestattet, Holzstaub und Reste findet man vergebens auf dem Boden. Wir sind zum Glück 2x durch den Produktionsprozess gelaufen und konnten beim ersten mal Staunen und beim zweiten mal gezielt mit Fragen und Erklärungen die abläufe kennenlernen.
Die Arbeitsprozesse selbst beginnen neben dem Auftrennen des Holzes mit dem Hobeln der Hals-Einzelteile. Bevor dieser Prozess beginnt, wird jedoch noch einmal die Feuchte des Holzes ermitteln und aussortiert sollte es über 10% oder unter 7% liegen. Zusätzlich dazu werden die Hölzer noch nach Ihrem Feuchtegehalt grob markiert um in der Montage nur Holzer mit Gleichem Feuchte Gehalt zu verleimen und so das unterschiedliche Arbeiten der Holzer in den Jahren als Instrument zu minimieren. Seit der Einführung 2009 ist die Reklamation durch Veränderung des Holzes somit auf fast 0% zurückgegangen. Für die Zukunft soll darüber hinaus noch geplant werden, dass Hölzer und Ihre Informationen über Feuchte und Gewicht gespeichert werden und genau dem jeweiligen Instrument zugeordnet werden können. So kann bei Reklamation festgestellt werden, was ggf. schiefgelaufen ist.
Der nächste Schritt ist das Verleimen und Zusammensetzen des Halses. Aus einem so verleimten Hals entstehen übrigens 2 Hälse, die gespiegelt zueinander im Betrieb zusammengesetzt und am Ende getrennt werden. Beim Zusammensetzen wird darauf geachtet stehende und liegende Jahresringe zueinander zu verleimen. Auch beim Anheften der Kopfplattenflügel wird auf die Jahresringe und eine möglichst ähnliche Farbe geachtet um die Auffälligkeit zu minimieren. Neben dem Halsspannstab kommen noch 2 zusätzliche Versteifungen zwischen dem 12-21/24 Bund um Verformungen in diesem Bereich, bedingt durch den Zug zwischen Verschraubung und den gespannten Saiten zwischen Brücke und Mechaniken zu vermeiden. Neben den Fräsmaschinen die bedingt durch den Einsatz von 5-fach Fräsern genaueste arbeiten beim Fräsen der Hälse und Bodys erreichen ist der Nächste große schritt sicherlich die Bundier- und Abrichtmaschine. Bei einem Einkaufspreis von 900k arbeitet sie mittlerweile seit 3 Jahren an den Hälsen der Warwick Bässe und Framus Gitarren. Fertig eingestellt ist sie noch nicht da sie im letzten Arbeitsschritt immer noch Fehler verursacht. Dazu im nächsten Absatz aber mehr.
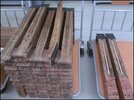
Das Ziel und der Grund für die Anschaffung dieser Maschine war es den Arbeitsschritt der Halsbearbeitung zu perfektionieren, also das Schleifen des Radius, das Bundieren und das Abrichten. Für den kompletten Durchgang eines Halses benötigt die Maschine ca. 30 Minuten. Dabei wird zuerst der Radius des Griffbrettes angepasst und anschließend die Maße des Griffbrettes maschinell bestimmt, die Bundschlitze oberflächig eingesägt und anschließen dem Griffbrettradius folgend gefräst. Weitere Schritte sind das einsetzen der vorgebogenen Bünde, das testen selbiger unter Halsspannung, das Ausmessen, Bohren und Einsetzen der Side-Dots und im letzten Schritt das Abrichten der Bünde. Letzteres funktioniert aber noch nicht fehlerfrei und wird für die Framus Gitarren noch mit dem Plek Verfahren durchgeführt.
Lackierung
Die Lackierhalle ist sicherlich ein eigenes Thema und ich hoffe das meine Mitbesucher etwas gezielter auf Einzelheiten eingehen werden/können als Ich. Die dort gebaute Lackiererei mit Anschaffungskosten von 1,4 Mio. wirkt nicht wirklich als würde dort lackiert werden. Man findet weder Farbe auf dem Boden, den Wänden oder sonst wo abgesehen von den Bässen und es riecht auch nicht nach Lack. Dieses ist sicherlich der guten Lüftung und dem auf Wasserbasis verwendeten UV-Lack zuzuschreiben.
Zum Trocknen wird das Instrument in eine Kammer mit durchströmendem Stickstoff gegeben um das UV-Licht so weit zu brechen, dass es auch jede kleine Ecke und Rundung des Instrumentes erreicht. Zudem wurde der Lack in den letzten Jahren weiterentwickelt/verändert und das merkt man in mehrfacher Hinsicht. Die Dicke des Lackes ist von 2-3mm auf unter 1mm gesenkt worden und dies merkt man, wenn man die Instrumente in die Hand nimmt.
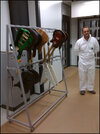
Interessant war auch zu erfahren, dass die Härte des Lackes am Ende so stark war, dass diese sogar wieder verringert werden musste, da das Schleifen vor dem Polieren nicht mehr ohne Probleme möglich war. Das die Härte aber immer noch mehr als ausreichend ist wurde uns durch das Kratzen mit einer Uhr auf dem Lack bewiesen.
Endmontage
Als wir die Endmontage erreichten standen dort natürlich schon wieder ein paar Bässe herum die uns natürlich nicht davon abhalten konnten sie uns etwas genauer anzusehen. Trotzdem hörten wir natürlich den Erklärungen weiter zu und erhielten weitere Einblicke in die überragende Qualität der dort gebauten Instrumente. So wird z.B. die Halstasche nicht weiter gefräst, als es unbedingt sein muss und der Hals schon mit etwas Mühe hinein oder hinausbewegt werden muss. Auch die Befestigung der Tonabnehmer mit einem Holzdübel welche ein Maschinengewinde im inneren hat für die PickUp schraube und einer Federung im Gegensatz zu einem Schwamm als Abstandshalter beeindruckten.
Nach der Endmontage und einer letzten Qualitätskontrolle wird dann auch die Seriennummer auf das Instrument gelasert. Fertig ist der Warwick Bass!
Furnieren
Am zweiten Tag bekamen wir dann noch einen Einblick in die Technik des Furnierens und wie Warwick es schafft, dieses ohne sichtbare Leimfuge zu verbinden. Dabei werden die Furniere zunächst gestanzt, um keine sichtbaren und ausgerissenen kanten zu hinterlassen. Im nächsten Schritt werden die Furniere innerhalb einer Maschine verleimt, ohne eine sichtbare Leimfuge zu hinterlassen.
Die Zargen werden soweit es möglich ist bei den halbakustischen Instrumenten aus Massivholz gefertigt und in Form gepresst. Um die Decken und Zargen ohne sichtbare Leimfuge zu verbinden, wird ein Rahmen auf die Decke gesetzt, an dessen Rand die Zarge passgenau angeleimt wird.
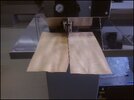
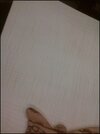
Ausflug in eine andere Welt
Nach der Führung durch das Werk durften wir natürlich auch in den Showroom und Bässe anspielen. Genug Auswahl und das passende Instrument war sicherlich für jeden von uns dabei. 4-, 5-, 6-, 8-, 12-Saiter Bässe als Righthand Version und einige Linkshänder Versionen waren so weit zu sehen und spielen. Im abgetrennten Raum standen dann die Warwick BC Serie und ein Hellborg Verstärker sowie 2 Framus Gittarenamps. Der Boden war mit Dunlop und Source Audio Effekten ausgestattet so das auch dort der ein oder andere Test möglich war. Dies nutzten Ratking, Goas und meine Wenigkeit am zweiten Tag auch gerne in aus und testen des Bass Fuzz Deluxe von MXR. Ein schönes Pedal

.
Ansonsten war natürlich das Auftreten von Jonas Hellborg und die Erklärung seines Amps, seines Systems und die Unterschiede zwischen diesem Verstärker und seinen Ansprüchen, bezogen auf herkömmliche Verstärker ein weiteres Highlight.
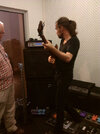
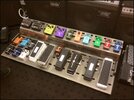
Die Eindrücke, die an diesem Tage auf uns wirkten und auf mich waren sehr viele, die aber gerne aufgenommen wurden. Man möge mir also verzeihen, wenn ich einiges nicht 100% wiedergegeben habe oder wichtige Fakten eurer Meinung nach vergessen habe, hehe

.
Framus Museum
Der Besuch das Framus Museums mit der Führung soll natürlich nicht komplett unerwähnt bleiben, der uns dort gebotene Einblick in die Geschichte der Firma Framus über die verschiedene Jahrzehnte war interessant und auch welche Neuigkeiten und Techniken angewendet wurden.
Grillabend
Der Grillabend am Montag war auch bedingt durch die doch zahlreichen Warwick Mitarbeiter die sich beteiligt haben ein guter Abschluss dieses Tages und gab uns natürlich die Möglichkeit sich mit den verschiedenen Mitarbeitern zu unterhalten und Fragen zu stellen. Dies nutzten wir am Ende des Tisches auch gut aus und lauschten Hans Peter Wilfer, Swen Klipphahn oder Michael Bär welcher bei uns gesessen hat und uns nebenbei noch den Einheimischen Kräuterschnaps zeigte. Es war eine rundum ungezwungene Atmosphäre, bei der es wirklich nicht so aussah, als hätte man sich gerade eben mal so getroffen und müsste jetzt hier sein.
Fazit: Für den Moment bleibt mir nur zu sagen das ich diesen Ausflug als sehr schön und informativ angesehen habe. Es war richtig nett bei Warwick und auch unter den Mitgliedern des Boards.
Mit freundlichen Grüßen
13 / Leif
Ich werde den Text später noch ein weiteres mal lesen und erneut auf Fehler kontrollieren. Vielleicht werde ich auch noch etwas zum Thema Energie schreiben und kontrollieren ob ich nicht noch zahlen/Dinge notiert habe die ich noch einbauen kann.