
Uli
Mod Emeritus
Um mich auch in einer relativ lauten Band trotz 600W im Proberaum noch zu jeder Zeit einwandfrei hören zu können, habe ich beschlossen, die diesjährige Winterpause dazu zu nutzen, mir eine Vibrationsplatte als Bass-Monitor zu bauen. Ähnliche Projekte wurden hier und in anderen Foren auch schon vorgestellt, manche davon wurden allerdings gar nicht zu Ende geführt und manche mit bestimmten Herangehensweisen, die ich lieber nicht kopieren möchte. Ich habe insofern versucht, das Beste aus allen Projekten, die ich in der Art finden konnte, zu recherchieren und dabei auch das am Markt erhältliche industrielle Vorbild nicht außer Acht gelassen. Den mehrfach gelesenen Wunsch, eine nachbaufähige Anleitung mit Preis- bzw Stückliste zu veröffentlichen, werde ich ebenfalls versuchen zu berücksichtigen... die Liste kann ich allerdings erst am Ende der Aktion erstellen, wenn ich alle Teile beisammen habe. Ein paar eigene Ideen sind natürlich auch noch eingeflossen... los gehts!
Das Prinzip der Shakerplatte beruht auf der Verwendung Vibration erzeugender Bauteile, die vom Wirkprinzip her ähnlich arbeiten wie Lautsprecher, nur daß hier die Schwingungen nicht auf eine Membrane übertragen werden, sondern auf ein Gewicht, das als Schwungmasse dient. Dadurch überträgt sich dessen Schwingung auf den jeweiligen Körper, an den das Shaker-Element angeschraubt ist, in diesem Fall die Platte, auf der der Bassist hinterher stehen wird. Heimkino-Liebhaber schrauben sich solche Shaker-Elemente auch gerne mal unter die Couch, von der aus sie dann ihre Hollywood-Katastrophen betrachten, wahrscheinlich kommt die Entwicklung auch eher aus diesem Sektor und die Verwendung als Bass-Monitor ist eher ein ungeplanter Seiteneffekt. Die von mir verwendeten Shaker können mit bis zu 100 Watt pro Stück beschickt werden und haben eine Impedanz von 4 Ohm, so daß sich bei Verwendung von vier Stück auch wieder eine Gesamtimpedanz von 4 Ohm ergibt, wenn man je 2 in Reihe geschaltete (à 8 Ohm) parallel schaltet.
Ein Aspekt für den Selbstbau sind sicher die Kosten, die bei höchstens etwa einem Drittel des Original Boards liegen, das anfangs von TechAmp und mittlerweile von Eich Amplification vertrieben wird. Ein Drittel der Kosten bedeutet allerdings, daß es trotzdem noch mit mindestens 150EUR zu Buche schlägt, sofern man nicht einiges an Material bereits zu Hause hat. Wie immer ist (bei mir) aber auch ein weiterer Aspekt der Spaß am Selbermachen, der im Winter witterungsbedingt meist auf inhäusige Projekte begrenzt ist. Sollte sich wider Erwarten rausstellen, daß die Verwendung des Shaker-Boards (für mich) doch nicht so der Bringer ist, habe ich wenigstens kein Vermögen in den Sand gesetzt...
Bei den Abmessungen habe ich mich an dem kleineren (S) Industrie-Board orientiert, dessen Grundfläche 55x80cm beträgt, die Höhe wird bei meinem Modell im Wesentlichen vom verwendeten Plattenmaterial und den die Distanz zwischen Boden- und Trittplatte bildenden Bauteilen bestimmt. Da ich mich da noch nicht festlegen will, habe ich mir außer der Boden- und der Trittplatte noch ein weiteres Stück Birke Multiplex schneiden lassen, aus dem ich nachher selbst die Zargen in der tatsächlich erforderlichen Breite sägen werde.
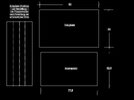
Als Plattenmaterial habe ich wie gesagt Birkensperrholz in 9mm Stärke gewählt, diese Mindeststärke ergibt sich aus der Länge der Gewinde-Einschlaghülsen (8mm), die ich für die Befestigung der Shaker verwenden werde und die komplett im Holz verschwinden müssen. Obwohl Birke zu den Harthölzern zählt, ist die Materialdichte geringer als bei Span- oder Siebdruckplatten... insofern ist es auch leichter... und teurer. Während bei Siebdruckplatten das hohe Gewicht durch die Tränkung der Holzplatten mit Kunstharz zustande kommt, ist es bei Spanplatten der hohe Leimanteil. Spanplatten eignen sich auch eher weniger in Anwendungen, die ständiger Erschütterung oder Vibration ausgesetzt sind, auch neigen sie beim Bearbeiten (z.B. bei der Verwendung von Einschlagmuttern) zum Ausreißen oder Brechen.
Ich werde 4 Shaker-Elemente verbauen, die von unten an die Trittplatte geschraubt werden und mittels Gummi-Schwingungsdämpfern auf Abstand zur Bodenplatte gehalten werden, so daß die Trittplatte praktisch frei über der Bodenplatte schwebt, also nur die Berührungspunkte mit den Gummipuffern hat.
Die später oben liegende Trittplatte habe ich wie gesagt auf die Maße des Industrie-Vorbildes sägen lassen: 80 x 55cm. Die Bodenplatte muß etwas kleiner sein, da sie praktisch in den "Kasten" hineinragen wird, der durch das spätere Anleimen der seitlichen Zargen (Maße hängen von der Länge der verwendeten Schwingungsdämpfer ab) entstehen wird, ohne diesen aber zu berühren. Sie beträgt 52,5 x 77,5cm - mit ihr fange ich an.
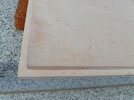
Zunächst ermittle ich durch ein Diagonalkreuz die Mitte und zeichne jeweils 8cm von der Ecke entfernt die Löcher an, an denen die Gummi-Schwingungsdämpfer angeschraubt werden.
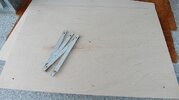
Diese Löcher müssen jetzt deckungsgleich auf die größere - die spätere Trittplatte - übertragen werde, was durch einfaches Durchbohren erfolgt, nachdem die Platten exakt ausgerichtet und gegen Verschieben gesichert sind. Bei beiden Platten markiere ich eine der Längsseiten, damit sie später bei der Montage wieder genauso liegen wie bei der Planung.
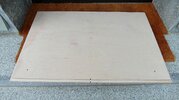
In die untere Bodenplatte kommen später noch das Anschlußpanel und beim Original ist dort auch der Tragegriff eingesetzt. Ob ich letzteren genau so übernehme, weiß ich noch nicht. Der Vorteil für diese Position des Griffes ist die Tatsache, daß er an dem nicht schwingenden Teil sitzt und sich daher nicht so leicht von selbst lösen sollte. Der Nachteil ist, daß das Konstrukt mit diesem seitlich angebrachten Griff nicht sonderlich gut ausbalanciert ist weil die schweren Shaker alle an der Trittplatte befestigt sind es und beim Transport vermutlich immer schief hängen wird.
An die obere Trittplatte kommen wie gesagt die Shaker dran, die Vorbereitung dafür wird der nächste Schritt.
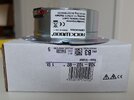
Das Prinzip der Shakerplatte beruht auf der Verwendung Vibration erzeugender Bauteile, die vom Wirkprinzip her ähnlich arbeiten wie Lautsprecher, nur daß hier die Schwingungen nicht auf eine Membrane übertragen werden, sondern auf ein Gewicht, das als Schwungmasse dient. Dadurch überträgt sich dessen Schwingung auf den jeweiligen Körper, an den das Shaker-Element angeschraubt ist, in diesem Fall die Platte, auf der der Bassist hinterher stehen wird. Heimkino-Liebhaber schrauben sich solche Shaker-Elemente auch gerne mal unter die Couch, von der aus sie dann ihre Hollywood-Katastrophen betrachten, wahrscheinlich kommt die Entwicklung auch eher aus diesem Sektor und die Verwendung als Bass-Monitor ist eher ein ungeplanter Seiteneffekt. Die von mir verwendeten Shaker können mit bis zu 100 Watt pro Stück beschickt werden und haben eine Impedanz von 4 Ohm, so daß sich bei Verwendung von vier Stück auch wieder eine Gesamtimpedanz von 4 Ohm ergibt, wenn man je 2 in Reihe geschaltete (à 8 Ohm) parallel schaltet.
Ein Aspekt für den Selbstbau sind sicher die Kosten, die bei höchstens etwa einem Drittel des Original Boards liegen, das anfangs von TechAmp und mittlerweile von Eich Amplification vertrieben wird. Ein Drittel der Kosten bedeutet allerdings, daß es trotzdem noch mit mindestens 150EUR zu Buche schlägt, sofern man nicht einiges an Material bereits zu Hause hat. Wie immer ist (bei mir) aber auch ein weiterer Aspekt der Spaß am Selbermachen, der im Winter witterungsbedingt meist auf inhäusige Projekte begrenzt ist. Sollte sich wider Erwarten rausstellen, daß die Verwendung des Shaker-Boards (für mich) doch nicht so der Bringer ist, habe ich wenigstens kein Vermögen in den Sand gesetzt...
Bei den Abmessungen habe ich mich an dem kleineren (S) Industrie-Board orientiert, dessen Grundfläche 55x80cm beträgt, die Höhe wird bei meinem Modell im Wesentlichen vom verwendeten Plattenmaterial und den die Distanz zwischen Boden- und Trittplatte bildenden Bauteilen bestimmt. Da ich mich da noch nicht festlegen will, habe ich mir außer der Boden- und der Trittplatte noch ein weiteres Stück Birke Multiplex schneiden lassen, aus dem ich nachher selbst die Zargen in der tatsächlich erforderlichen Breite sägen werde.
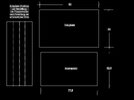
Als Plattenmaterial habe ich wie gesagt Birkensperrholz in 9mm Stärke gewählt, diese Mindeststärke ergibt sich aus der Länge der Gewinde-Einschlaghülsen (8mm), die ich für die Befestigung der Shaker verwenden werde und die komplett im Holz verschwinden müssen. Obwohl Birke zu den Harthölzern zählt, ist die Materialdichte geringer als bei Span- oder Siebdruckplatten... insofern ist es auch leichter... und teurer. Während bei Siebdruckplatten das hohe Gewicht durch die Tränkung der Holzplatten mit Kunstharz zustande kommt, ist es bei Spanplatten der hohe Leimanteil. Spanplatten eignen sich auch eher weniger in Anwendungen, die ständiger Erschütterung oder Vibration ausgesetzt sind, auch neigen sie beim Bearbeiten (z.B. bei der Verwendung von Einschlagmuttern) zum Ausreißen oder Brechen.
Ich werde 4 Shaker-Elemente verbauen, die von unten an die Trittplatte geschraubt werden und mittels Gummi-Schwingungsdämpfern auf Abstand zur Bodenplatte gehalten werden, so daß die Trittplatte praktisch frei über der Bodenplatte schwebt, also nur die Berührungspunkte mit den Gummipuffern hat.
Die später oben liegende Trittplatte habe ich wie gesagt auf die Maße des Industrie-Vorbildes sägen lassen: 80 x 55cm. Die Bodenplatte muß etwas kleiner sein, da sie praktisch in den "Kasten" hineinragen wird, der durch das spätere Anleimen der seitlichen Zargen (Maße hängen von der Länge der verwendeten Schwingungsdämpfer ab) entstehen wird, ohne diesen aber zu berühren. Sie beträgt 52,5 x 77,5cm - mit ihr fange ich an.
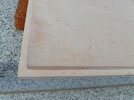
Zunächst ermittle ich durch ein Diagonalkreuz die Mitte und zeichne jeweils 8cm von der Ecke entfernt die Löcher an, an denen die Gummi-Schwingungsdämpfer angeschraubt werden.
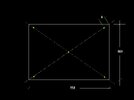
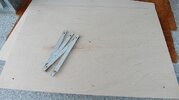
Diese Löcher müssen jetzt deckungsgleich auf die größere - die spätere Trittplatte - übertragen werde, was durch einfaches Durchbohren erfolgt, nachdem die Platten exakt ausgerichtet und gegen Verschieben gesichert sind. Bei beiden Platten markiere ich eine der Längsseiten, damit sie später bei der Montage wieder genauso liegen wie bei der Planung.
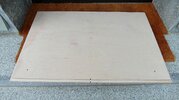
In die untere Bodenplatte kommen später noch das Anschlußpanel und beim Original ist dort auch der Tragegriff eingesetzt. Ob ich letzteren genau so übernehme, weiß ich noch nicht. Der Vorteil für diese Position des Griffes ist die Tatsache, daß er an dem nicht schwingenden Teil sitzt und sich daher nicht so leicht von selbst lösen sollte. Der Nachteil ist, daß das Konstrukt mit diesem seitlich angebrachten Griff nicht sonderlich gut ausbalanciert ist weil die schweren Shaker alle an der Trittplatte befestigt sind es und beim Transport vermutlich immer schief hängen wird.
An die obere Trittplatte kommen wie gesagt die Shaker dran, die Vorbereitung dafür wird der nächste Schritt.
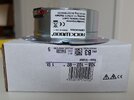
- Eigenschaft
Zuletzt bearbeitet: