F U C K !!!
Aber der Reihe nach... Nach endlosen Testhälsen (aus Abfallholz, meistens Fichtenregalbretter) hab ich mich also an den tollen Hals gewagt. SOOO lange habe ich darauf gewartet, gespart, mich gefreut und gebangt und am Ende (Achtung Spoiler) ging es ordentlich in die Hose...
So liegt das jungfräuliche Holz auf der CNC:
Dann die Indexlöcher gebohrt:
Dies hat mir in der Vergangenheit auch schon oft geholfen, um den Nullpunkt wieder zufinden. Das gelingt so ganz zuverlässig!
Dann habe ich angefangen mit der 3D-Kontur. Wenn ich mit der Außenkontur angefangen hätte, wäre das so eine schmale und SEHR tiefe Nut geworden. Die Spanabfuhr wäre schwierig geworden. Deswegen habe ich mich entschieden, zuerst die 3D-Kontur der Halsrückseite zu schruppen. Dabei musste ich mit ganz seltsamen Parametern fahren: 8er Fräser, nur 4mm eingetaucht, 600mm/min Vorschub und die Drehzahl nur auf ca. 2.5. Das war ein seeehr feinfühliges Gleichgewicht. Drehe ich die Drehzahl hoch, werden die Späne innerhalb von Sekunden schwarz und fangen sogar an zu glimmen! Drehe ich die Drehzahl runter wird es sehr ruppig und hakelig. Bei tieferen Eintauchversuchen und schnellerer oder langsamerem Vorschub habe ich keinen passenden "Sweetspot" gefunden. So musste ich die Fräsparameter also "on the go" testen, das war unangenehm. Andererseits sind die ersten paar Meter Fräsweg hier beim schruppen fürs Endergebnis recht egal. Also konnte ich munter Parameter ausprobieren, bis es halbwegs passte.
Dann mal die Kontur gefräst, allerdings nur bis 36mm Tiefe (insgesamt ist das Halsholz 46mm dick!). Und den Fräsdurchmesser hab ich auf 10mm gestellt, obwohl ich mit einem 8er Fräser fräse. So fräse ich mit 1mm Offset. Da macht es nichts, wenn das Holz schwarz wird oder es ein paar Ausrisse gibt.
Tiefer hab ich mich dann nicht mehr getraut, weil eben die Spanabfuhr schwierig wurde.
Deswegen habe ich den Hals dann nochmal von der Fräse runtergenommen und die Seitenteile mit verschiedenen Japansägen abgesägt. Eine Bandsäge hab ich leider nicht.
Danach also den Hals wieder auf die CNC, 0-Punkt kontrolliert und dann die Kontur fertig gefräst. Danach ein weiteres Mal die Kontur gefräst, dieses Mal mit 8mm Fräsdurchmesser, 10mm Zustellung, 1000mm/min Vorschub und deutlich höherer Drehzahl (Stufe 5 ungefähr). Im Bild sieht man rechts am Halsfuß, wie der letzte mm abgenommen wird:
Danach mit dem gleichen 8er Fräser geschlichtet. Experimente mit dem Kugelfräser mach ich wann anders mal. War jetzt froh, dass es so gut lief. Die linke Hälfte ist geschlichtet, die rechte ist noch grob geschruppt:
So sah der Hals dann nach dem Schlichten aus:
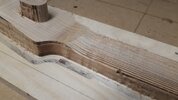
Und ich sah, dass es gut war
Und dachte mir: Toll, alles schwierige ist geschafft, jetzt "nur noch schnell" der Skunkstripe. Ein Fräsprogramm von 6 min.
Sah auf den ersten Blick auch gut aus... Bis ich die Späne aus der Nut saugte...
F U C K !!!
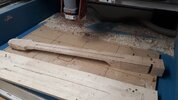
So eine riesen Scheiße...
Beim Saugen der Späne sah ich schon, dass da das Holz der Unterlage zum Vorschein kam... Offensichtlich hatte sich der Fräser etwas gelöst und ist in der Spannzange weiter rausgerutscht... Klar, es hätte auch was schlimmeres passieren können.
Aber insgesamt bin ich jetzt schon RICHTIG niedergeschlagen. Ich fand das Halsholz so toll!!! Und jetzt? Vlt wäre es am besten, einfach einen neuen Hals zu machen. Andererseits hab ich ja mit GENAU DEM Halsholz schon das Holzbinding für den Korpus gesägt, gefräst und gebogen. Und das hat so gut geklappt! Das würde ich auch gerne verwenden...
Überlege, ob ich vlt einfach doch mit Griffbrett baue... das wäre die einzige Rettungsmöglichkeit. Dabei finde ich one-piece-maple so cool.. *heul*
Heute abend ist mir jedenfalls einfach nur zum Heulen zumute. So eine Kacke... Sowas darf doch nicht passieren... :-(