
Luebbe
Registrierter Benutzer
Baubericht Teil 1
Nachdem mein letzter Eigenbau fast 2 Jahre her ist, konnte ich mich langsam dem wiederkehrenden Baufieber nicht mehr erwehren.
Die Frage war nur: Was baue ich?
Vor ca. 1,5 Jahren habe ich mit dem Kontrabassspielen angefangen. Seit ca. 1 Jahr spiele ich auch in einer passenden Jazz-Combo mit, wobei mein Können auf dem KB dafür eigentlich noch nicht ausreicht. Zudem habe ich schnell feststellen müssen, dass der Transport von dem Teil immer ein ganz schöner Act ist. Daher kam mir die Idee einen Electric Upright zu kaufen oder zu bauen. Allerdings ist so ein Teil ja nichts halbes und nichts ganzes, daher viel mein Entschluss aufs halbe zu gehen und einen E-Bass zu bauen, allerdings lined Fretless, um wenigstens mein Gehör für den Kontrabass zu trainieren.
Die Anzahl der Saiten sollte auch zum Kontrabass passen, also ein 4-String.
Bei den Hölzern verwende ich ja eigentlich immer gerne heimisches Holz, ich wollte allerdings für einen Fretless unbedingt ein Ebenholz-Griffbrett haben. Der Rest sollte dann eher schilicht werden, Mehrstreifiger Ahorn Hals und ein Korpus aus Erle.
Ansonsten wollte ich eher ein modernes Design haben. Ich verrate mal nicht, wo ich diesmal abgekupfert habe. Mal sehn, wer es als erster errät. Als besondere Herausforderung habe ich mir eine abgewinkelte Kopfplatte vorgenommen.
Auf dem folgenden Bild sieht man mal das Rohmaterial.
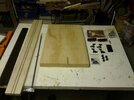
Wie man sieht soll es schwarze Hardware mit Kluson Mechaniken werden. Die Pickups sind ein DiMarzio DP123 Set. Als Elektronik kommt eine aktive Artec Elektronik mit 3-Band-EQ zum Einsatz.
Als erstes sollte es ans absägen und anschäften der Kopfplatte gehen. Dafür hab ich mir eine Japansäge gekauft (tolles Werkzeug) und damit versucht einen möglichst geraden Schnitt hinzubekommen.
Von vorne sieht's ganz gut aus:
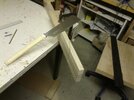
Die Rückseite hat aber leider nicht so toll geklappt:
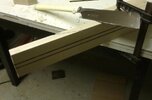
Da ich keine geeigneten Hobelmaschinen oder ähnliches besitze, musste ich mir für die Nachbearbeitung eine Vorrichtung für die Oberfräse Bauen:
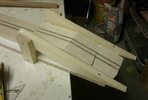
Um dann anschließend mit der Fräse...
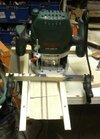
... für eine einigermaßen ebene Fläche im gewünschten Winkel zu sorgen. Hier sieht man das Ergebnis:
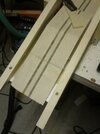
Als nächstes musste die Kopfplatte noch in ihrer Dicke von ca. 25 mm auf 14 mm reduziert werden. Dazu habe ich ein ganz ähnliche Vorrichtung gebaut und in 2-3 mm Schritten die Kopfplatte auf die richtige Dicke gebracht:
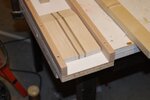
Anschließend konnte die Kopfplatte an den Rest vom Hals wieder angeleimt werden. Hierbei ist es bei dem mehrstreifigen Hals wichtig, dass die Streifen genau passend aneinander geleimt werden, sonst sieht's sch*** aus.
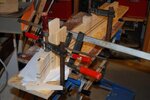
Das Problem dabei war, dass ich die Streifen nur auf der Rückseite kontrollieren konnte, da auf der anderen Seite die Zwingen die Sicht blockiert haben. Im Ergebnis haben auf der Griffbrettseite die Streifen nicht richtig gepasst. Dieser Effekt wird später zum Glück vom Griffbrett verdeckt.
Nachdem mein letzter Eigenbau fast 2 Jahre her ist, konnte ich mich langsam dem wiederkehrenden Baufieber nicht mehr erwehren.
Die Frage war nur: Was baue ich?
Vor ca. 1,5 Jahren habe ich mit dem Kontrabassspielen angefangen. Seit ca. 1 Jahr spiele ich auch in einer passenden Jazz-Combo mit, wobei mein Können auf dem KB dafür eigentlich noch nicht ausreicht. Zudem habe ich schnell feststellen müssen, dass der Transport von dem Teil immer ein ganz schöner Act ist. Daher kam mir die Idee einen Electric Upright zu kaufen oder zu bauen. Allerdings ist so ein Teil ja nichts halbes und nichts ganzes, daher viel mein Entschluss aufs halbe zu gehen und einen E-Bass zu bauen, allerdings lined Fretless, um wenigstens mein Gehör für den Kontrabass zu trainieren.
Die Anzahl der Saiten sollte auch zum Kontrabass passen, also ein 4-String.
Bei den Hölzern verwende ich ja eigentlich immer gerne heimisches Holz, ich wollte allerdings für einen Fretless unbedingt ein Ebenholz-Griffbrett haben. Der Rest sollte dann eher schilicht werden, Mehrstreifiger Ahorn Hals und ein Korpus aus Erle.
Ansonsten wollte ich eher ein modernes Design haben. Ich verrate mal nicht, wo ich diesmal abgekupfert habe. Mal sehn, wer es als erster errät. Als besondere Herausforderung habe ich mir eine abgewinkelte Kopfplatte vorgenommen.
Auf dem folgenden Bild sieht man mal das Rohmaterial.
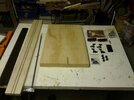
Wie man sieht soll es schwarze Hardware mit Kluson Mechaniken werden. Die Pickups sind ein DiMarzio DP123 Set. Als Elektronik kommt eine aktive Artec Elektronik mit 3-Band-EQ zum Einsatz.
Als erstes sollte es ans absägen und anschäften der Kopfplatte gehen. Dafür hab ich mir eine Japansäge gekauft (tolles Werkzeug) und damit versucht einen möglichst geraden Schnitt hinzubekommen.
Von vorne sieht's ganz gut aus:
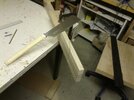
Die Rückseite hat aber leider nicht so toll geklappt:
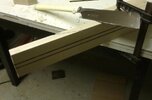
Da ich keine geeigneten Hobelmaschinen oder ähnliches besitze, musste ich mir für die Nachbearbeitung eine Vorrichtung für die Oberfräse Bauen:
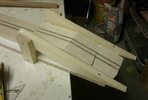
Um dann anschließend mit der Fräse...
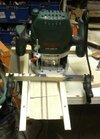
... für eine einigermaßen ebene Fläche im gewünschten Winkel zu sorgen. Hier sieht man das Ergebnis:
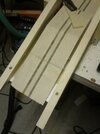
Als nächstes musste die Kopfplatte noch in ihrer Dicke von ca. 25 mm auf 14 mm reduziert werden. Dazu habe ich ein ganz ähnliche Vorrichtung gebaut und in 2-3 mm Schritten die Kopfplatte auf die richtige Dicke gebracht:
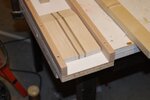
Anschließend konnte die Kopfplatte an den Rest vom Hals wieder angeleimt werden. Hierbei ist es bei dem mehrstreifigen Hals wichtig, dass die Streifen genau passend aneinander geleimt werden, sonst sieht's sch*** aus.
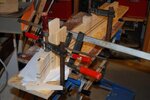
Das Problem dabei war, dass ich die Streifen nur auf der Rückseite kontrollieren konnte, da auf der anderen Seite die Zwingen die Sicht blockiert haben. Im Ergebnis haben auf der Griffbrettseite die Streifen nicht richtig gepasst. Dieser Effekt wird später zum Glück vom Griffbrett verdeckt.
- Eigenschaft